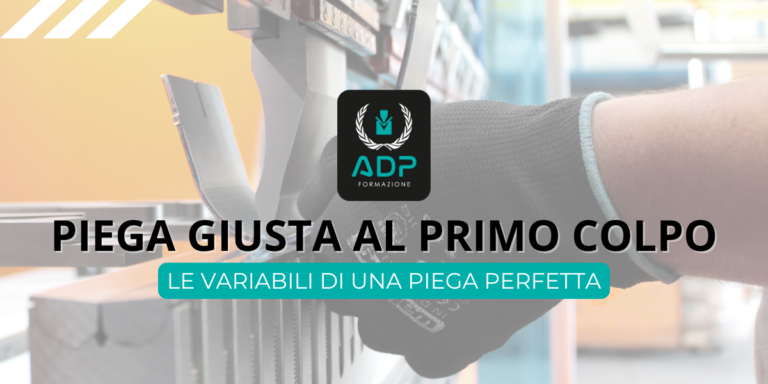
A pensarci bene non esiste comparto tecnologico che non abbia le sue “chimere”.
Parliamo di quel risultato “perfetto” ma difficilissimo da ottenere per una serie di concause fisiologiche.
Immaginiamo ciò che avviene nella messa a punto di un’auto da corsa: il massimo sarebbe ottenere velocità estreme unite ad una grande aderenza in curva, specie in determinati circuiti.
Ora, chiunque abbia seguito un minimo il mondo delle corse sa che per ottenere più o meno velocità e aderenza è necessario intervenire sul carico aerodinamico, però più carico significa maggiore aderenza, ma minore velocità e viceversa.
Avere tutte e due le cose è davvero un risultato complesso da raggiungere.
In piegatura uno dei sogni più inseguiti è, assieme agli sviluppi perfetti in ogni situazione di lavoro, la ripetibilità degli angoli di piega.
Gli operatori di lunga data lo sanno bene quanto è importante la collaborazione di chi viene prima di loro nella filiera produttiva.
Partiamo dall’inizio: una progettazione che tenga conto dei limiti fisiologici del processo è fondamentale per non costringere la produzione a lavorare con matrici dalle dimensioni ridotte.
Successivamente, anche coloro che dispongono i pezzi sulla lastra (fase di nesting) possono fare molto prediligendo un senso di laminazione costante, quando possibile, per tutti gli articoli identici e che devono essere piegati.
Anche chi scarica i pezzi dalla macchina di taglio ha una grande importanza: suddividere gli articoli per differente lamiera, senso di laminazione o pacco di lamiere è un grande aiuto per l’operatore che dovrà lavorare su una pressa tradizionale.
Senza scendere in maniera troppo approfondita nell’argomento è comunque molto interessante conoscere il perché la costanza d’angolo è così complessa da ottenere.
Il raggio interno: prendere o meno “una brutta piega”
Assodato il fatto che il valore del raggio interno è una semplificazione, in quanto non ha affatto un valore costante come quando il progettista modella in 3D: la sua grandezza è più o meno ampia man mano che aumenta la resistenza allo snervamento del materiale.
Più una lamiera è resistente, più il raggio interno diventa grande e viceversa.
È già possibile apprezzare il fenomeno con i materiali più largamente diffusi nelle carpenterie:
a parità di spessore e utensili adottati in alluminio, più cedevole sotto al punzone, tende a generare un raggio di piegatura ridotto rispetto all’acciaio al carbonio o, ancora di più, all’acciaio inossidabile Aisi304.
Secondo alcune osservazioni (fonte “The Fabricator”, autorevole sito statunitense che si occupa del mondo della manifattura) c’è una certa proporzionalità tra la grandezza del raggio interno e la resistenza del materiale.
Se, ad esempio, un acciaio dalla resistenza X genera un raggio di piega pari a 2 mm, un altro dello stesso spessore, piegato sui medesimi utensili ma dalla resistenza pari a 2X genera un raggio di circa 4mm.
Cosa genera un raggio interno
Per capire qual è il motivo per cui si genera un raggio interno rispetto ad un altro è necessario conoscere il fenomeno dell’incrudimento.
L’incrudimento è un fenomeno metallurgico che consiste nell’aumento della resistenza di un materiale soggetto ad una deformazione a freddo.
Immaginiamo una piegatura per fasi, concentrandoci esclusivamente sulla zona che viene deformata: quella piccola striscia di materiale esattamente sotto al punzone.
Non appena viene superato il punto di pinzamento e il ritorno elastico iniziale il materiale inizia a deformarsi.
Ciò significa che esattamente nella zona di deformazione vi è un aumento di resistenza: ciò costringerà le fibre a destra e a sinistra della linea incrudita ad essere coinvolte nella deformazione.
Ovviamente anche all’interno di esse avrà origine il fenomeno dell’incrudimento, per questo le fibre ulteriormente periferiche verranno coinvolte nella deformazione e così via.
Più incrudimento significa più resistenza e, di riflesso, un raggio interno più ampio.
Il limite geometrico della piegatura
Spesso non ci si rende conto, ma l’esatta quota del punto morto inferiore (il punto massimo di discesa della traversa o pestone) per ottenere una determinata piega avrebbe bisogno di una precisione molto alta.
Qualsiasi operatore può accorgersi di ciò semplicemente aggiungendo o togliendo un solo grado di correzione in fase di lavorazione di un pezzo: il valore del punto morto inferiore cambia di pochi decimi, quando non di pochi centesimi!
Ad esempio:
Con una matrice da V=16mm, tra 89° e 90° la differenza del PMI è sotto al decimo di millimetro.
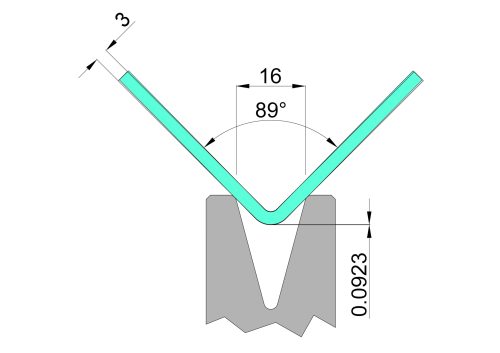
Ciò significa che è sufficiente trovarsi a lavorare un materiale di media qualità oppure uno spessore troppo elevato e che, quindi, presenta delle tolleranze più lasche per avere una costanza degli angoli di piega davvero scarsa.
Il senso di laminazione che dà raggi diversi
Se a materiali differenti corrispondono, come noto, anche valori di raggio interno diversi, ciò che è meno noto è che la stessa cosa capita tra differenti sensi di laminazione nello stesso materiale.
Esso è un fenomeno presente nei materiali molto anisotropici quali, ad esempio, alcune leghe di alluminio o l’Aisi 430.
Quando la linea di piega è perpendicolare al senso di laminazione il raggio interno di piega è più ampio e il materiale garantisce le proprie migliori prestazioni.
Viceversa, con una linea di piega parallela al senso di laminazione il raggio interno risulta ridotto.
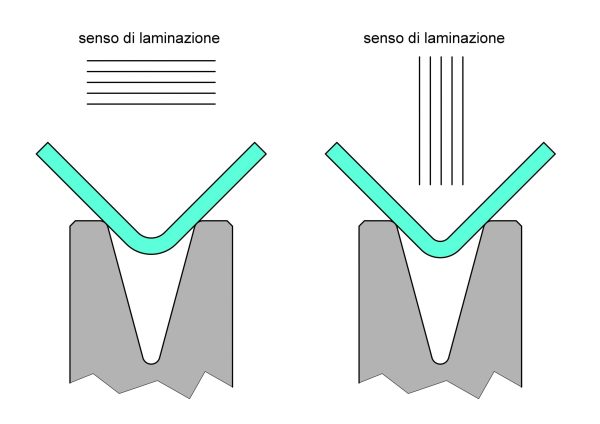
La costanza negli spessori: un altro brutto problema
In realtà, ancora prima dell’anisotropia appena descritta, la variabile primaria è la differenza di spessore tra un pezzo e l’altro.
Le lamiere possiedono delle tolleranze sugli spessori, ma risultano davvero troppo grossolane per la costanza d’angolo di cui il piegatore avrebbe bisogno.
Su una lamiera da 3 mm in S235, ad esempio, non è raro riscontrare spessori ben al di sotto della misura nominale, come 2,8mm o meno.
Immaginiamo di piegare sulla matrice da 16mm dell’esempio precedente due pezzi all’apparenza simili ma con 0,2 mm di differenza sullo spessore tra uno e l’altro: le pieghe saranno diverse di ben oltre i 2 gradi!
La tecnologia che aiuta
I costruttori di presse piegatrici, per lo meno quelli che hanno alle spalle un’importante esperienza e, soprattutto, la conoscenza del processo di piegatura (cosa affatto scontata, dal momento che fare una macchina e conoscere le problematiche di utilizzo non sono affatto la stessa cosa) hanno ormai impiegato da tempo diverse tecnologie per cercare di raggiungere al meglio la “chimera” del pezzo giusto “al primo colpo”.
La filosofia che va per la maggiore e oggigiorno la più efficace è quella di effettuare i controlli e le correzioni a valle del processo.
Ciò significa essere consci che in piegatura la certezza è fisiologicamente impossibile.
A dire la verità ci sono anche dei costruttori di tutto rispetto che non si limitano più a “leggere il risultato e correggere di conseguenza”, ma danno la possibilità di utilizzare un database di valori di ritorno elastico già presente in macchina e in grado di aggiornarsi di continuo.
Oggigiorno possedere un controllo dell’angolo, grazie al grandissimo miglioramento tecnologico degli ultimi tempi, garantisce una competitività spesso irrinunciabile.
Gli ultimi sistemi lanciati sul mercato permettono di lavorare sempre con meno limitazioni quali:
- riflettenza del materiale (tallone di Achille di diversi anni fa)
- bordi minimi di piega troppo lunghi
- angoli di piega molto acuti
Molti sistemi con un principio geniale in comune
Ogni costruttore che proponga un sistema di controllo dell’angolo è in grado di coprire egregiamente una determinata serie di lavorazioni sulla base del target a cui si rivolge.
Esistono sistemi più o meno adatti a certe situazioni e più o meno impegnativi dal punto di vista economico.
In generale, tuttavia, il principio è quello di mantenere non più una quota di punto morto inferiore fissa da raggiungere, bensì una quota “galleggiante”.
Arrivati in prossimità dell’angolo da realizzare ci sarà una breve fase di rilascio della pressione affinché il pezzo possa manifestare tutto il ritorno elastico accumulato.
È proprio grazie alla rilevazione attraverso differenti sistemi dell’angolo di apertura dovuto al ritorno elastico che verrà generata la correzione che si tramuterà in una seconda pressata.
Sarà proprio quest’ultima che permetterà di ottenere una precisione ed una costanza difficilmente raggiungibili altrimenti, il tutto con un ciclo davvero molto breve e talvolta impercettibile.
Diversamente, con l’ausilio di un database efficace di ritorni elastici anche il primo pezzo non necessiterà di una doppia pressata: si potrà ottenere un angolo di piega molto preciso “al primo colpo”.
Conclusioni
In conclusione, la “piega giusta al primo colpo” rimane una sfida complessa nel campo della piegatura della lamiera, influenzata da molteplici fattori come l’incrudimento del materiale, il senso di laminazione e le variazioni di spessore. Tuttavia, i progressi tecnologici stanno rendendo questo obiettivo sempre più raggiungibile. Le moderne presse piegatrici, equipaggiate con sistemi di controllo dell’angolo e database di ritorno elastico, offrono soluzioni innovative per migliorare la precisione e la ripetibilità. Mentre alcuni sistemi correggono l’angolo dopo la piega iniziale, altri utilizzano database avanzati per ottenere risultati accurati fin dal primo tentativo. Questi sviluppi non solo aumentano l’efficienza produttiva, ma riducono anche la necessità di correzioni successive, avvicinando l’industria all’ideale della “piega perfetta” che un tempo sembrava irraggiungibile.
Articolo pubblicato sulla rivista Lamiera edizioni Tecniche Nuove Ottobre 2021 (Focus Ottobre).
Hai bisogno di informazioni? Scrivi a emiliano@accademiadellapiegatura.it
Scarica gratis anche tu il nostro regolo di piegatura.